M.I.D.A.S - an Engineering Project
- Côme Serlooten
- Feb 4, 2022
- 3 min read
As a first year engineering student, we were expected to work on a project (a « T.I.P.E ») in teams of 2-3, over the course of a year, on a simple project of our choosing.
For our TIPE, my team and I decided to explore a project I had previously formulated : a hand mounted system that would get the position of the fingers of your hand in order for it to be usable by a computer.
MIDAS therefore stands for "Manual Indexing in Digital Applications and Software", which was a fun way for us to name it after the King Midas of legends, whose hand had the power to turn what it touched to gold.
We thought that this concept could be of use in many domains such as VR, robotics, animation, or even some medical applications. However before that we needed to map out the constraints we would have to face during this project. First of all, the glove-like structure had to be adjustable to account for different hand sizes. Then, it would need to be lightweight, if possible not to large to allow natural movements, and cheap. Lastly, we wanted to have it be able to transmit its data quick to allow real-time movements on the screen if possible.
The design we settled on was a 3D printed set of pieces forming a light plastic exoskeleton with moving parts to allow movement. On each articulation, a set of potentiometer captors was fixed and rotated when each articulation of a finger would bend.

1. Carboard and Cork Model of the design
Using this first design, we were able to start making progress on the rest of the process : making digital versions that we could exploit and experiment with better.
In order to display the hand movement in a demonstration, we thought of using Blender, which has an interface to animate through code and therefore allowed us to control a rig using info collected elsewhere.
Then, for the clean functional structure, we used SolidWorks to create an articulated model with defined mechanical constraints, allowing us to verify that once made into a physical design, all articulations would function as intended.


2. Blender Rig and SolidWorks model with key rotations indicated
We can notice on the SolidWorks model that the parts on the knuckes have two moving joints, sliding parts at the base of each finger to account for different hand sizes, and the thumb has more complex articulations as it has much more complex movements. All these details were thought to attempt more comfort for the wearer.
Ultimately, we ended up having to use relatively large captors for budget reasons, so they impeded the movement freedom of the MIDAS glove, but they did provide a simple enough output for us to use even though 3 wires were required for each to be connected to the Arduino Card we used as the "brain" of the
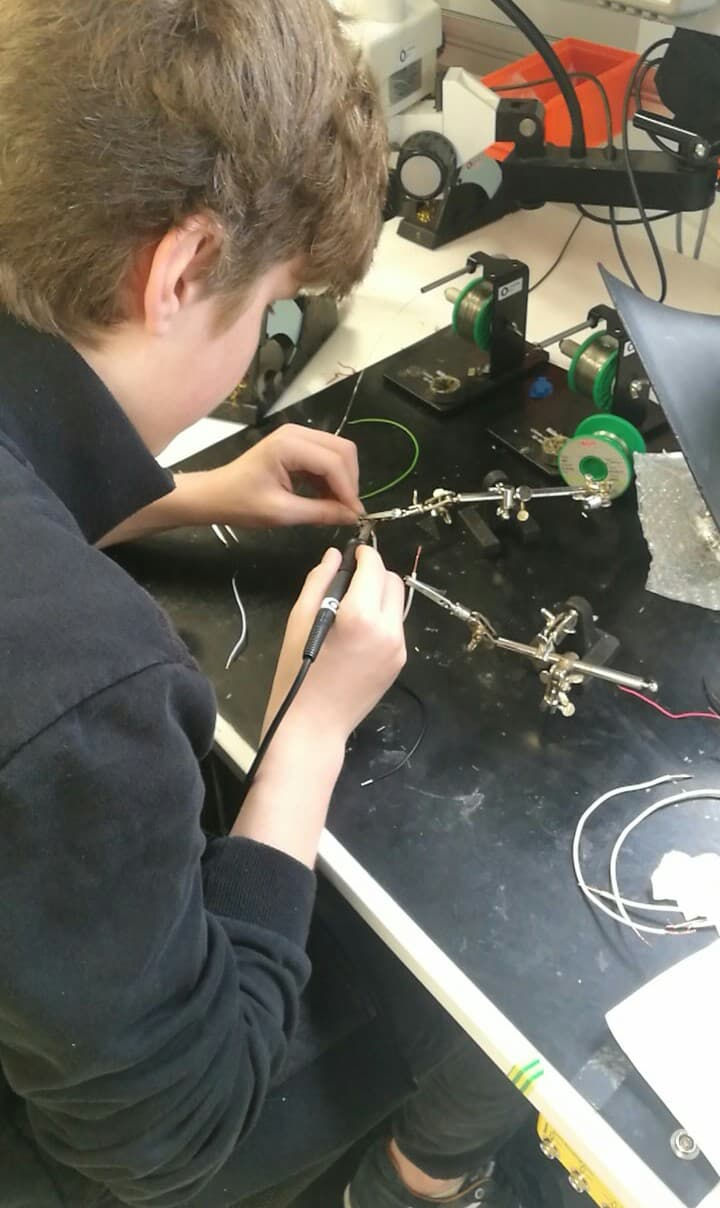
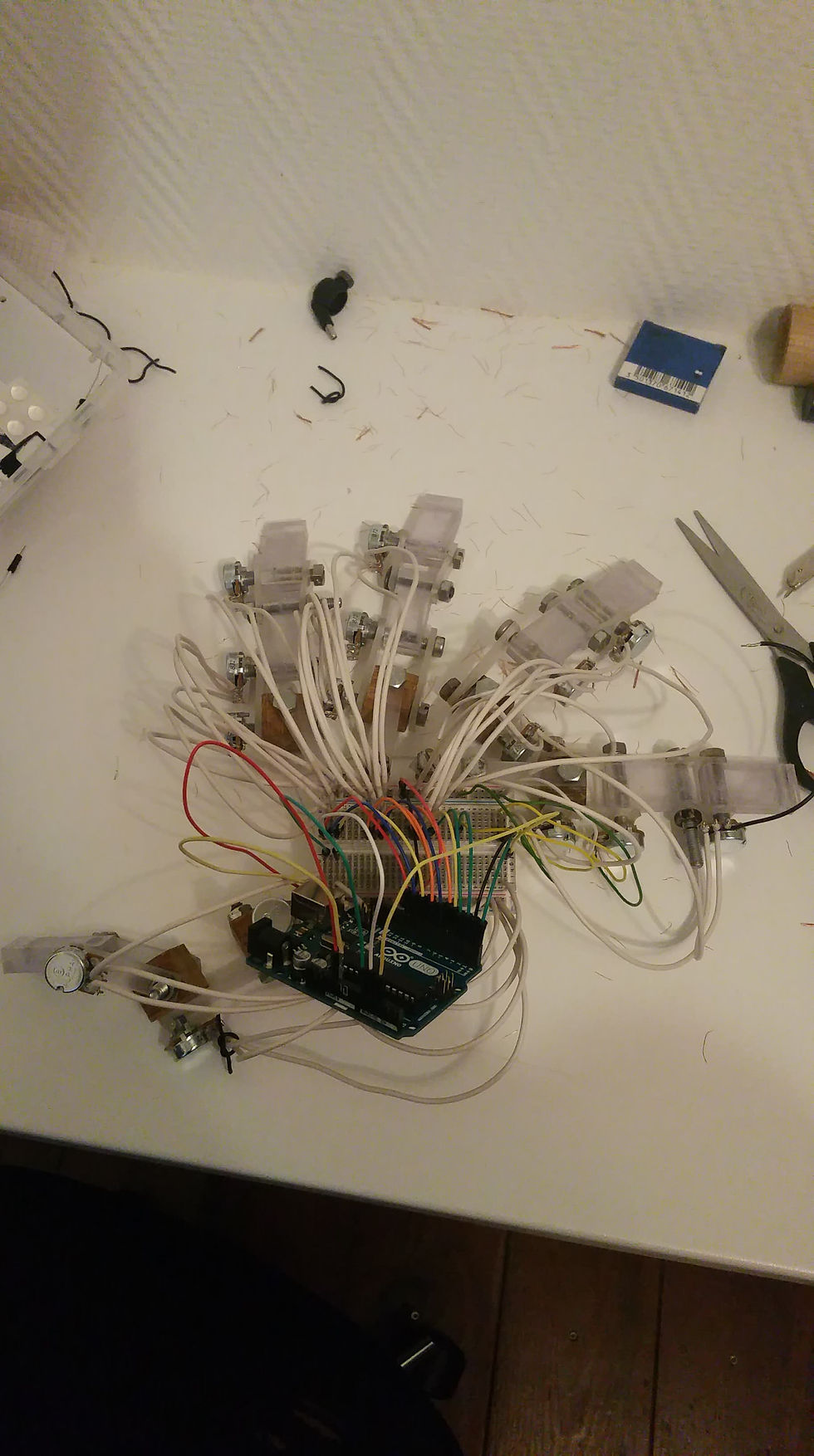
3. Soldering process of the wires and finished model with all captors connected
In the end the design ended up being had to use, and weakness in the wires made it unstable and not work 100% of the time. In fact, we understood after the deadline of the project that the issues came from wire short-circuiting each other and a misunderstanding of the Blender API.
However, a simple demo was still made as a proof of concept :
If you want more technical information on this project, you can read it up from our report :
Comments